半導体チップができるまでのプロセスをできるだけわかりやすく解説していきます。
半導体チップ製造業者(メーカー)になった視点でのお話になります。
なにか疑問点がありましたら、追記・補足を行いますので、お気軽にコメントかお問い合わせフォームからご連絡ください。
1.半導体製造装置メーカーから半導体製造装置を購入する
半導体チップを作るためには、半導体を作るための製造装置が必要になります。
製造装置無しでは半導体チップは1チップたりとも作ることができません。
特に、最先端の半導体チップはナノメートルオーダー(1/1,000,000,000m=10億分の1メートル)の非常に高い精度で加工をする必要があり、最先端の技術を詰め込んだ半導体製造装置が必要になります。
半導体製造のメーカー
半導体製造装置のメーカーは世界中に点在しており、数が非常に多いです。
主要メーカーは下記のとおりです。
・アプライドマテリアルズ(アメリカ)
・東京エレクトロン(日本)
・ラムリサーチ(アメリカ)
・ASML(オランダ)
・KLAテンコール(アメリカ)
・アドバンテスト(日本)
・SCREEN ホールディングス(日本)
・テラダイン(アメリカ)
・日立ハイテク(日本)
・ASMインターナショナル(オランダ)
・ニコン(日本)
・キャノン(日本)
・ディスコ(日本)
・東京精密(日本)
・キューリック・アンド・ソファ[KULICKE AND SOFFA INDUSTRIES, INC.](アメリカ)
・レーザーテック(日本)
2.ウエハを購入する
半導体チップの原材料はシリコン(Si)というものです。
シリコンは地球上に豊富に存在している物質です。
このシリコンという材料をそのまま工場に運んでも高性能は半導体チップは作ることができません。
シリコンの純度を高めて品質を高くする必要があるのです。
そのため非常に高温の炉の中にシリコンを入れてどろどろに溶かして、そこから種結晶というものを先端につけた棒を炉にツッコミ、上に引っ張り上げます。
そうすると、種結晶にドロドロのシリコンがひっついてくるのです。
これをゆっくりゆっくり実行して、高品質のシリコンの円柱状の塊が出来上がります。
この円柱状の片町のことをシリコン・インゴットと呼びます。
そして苦労して作り出した高品質なシリコン・インゴットを、よりたくさん使うために、ワイヤで輪切りに薄くスライスしていきます。
円柱状のシリコン・インゴットを輪切りにするので、非常に薄い円盤が出来上がります。
この薄いシリコンの円盤のことを「シリコン・ウエハ(Silicon Wafer」と呼びます。
ウエハは、英語でWaferと書きますので、ウエハといったり、ウェハといったり、ウエハーといったりしますが、同じ意味です。
シリコン以外にも、ゲルマニウム(Ge)など他にも半導体となる材料はありますが、単純にウエハというとシリコン(Si)を指す場合が多いです。
シリコン・ウエハを作っているメーカー
・信越化学工業(日本)
・SUMCO[サムコ](日本)
3.フォトマスクを設計する
半導体チップは、シリコンウエハに微細なパターンを形成することで作られます。
微細なパターンを形成するために必要になるのが、「フォトマスク」です。
シンプルに「マスク」と呼んだりすることもあります。
フォトマスクの使い方を解説しますと、
・シリコンウエハにレジスト(感光剤)を塗って、薄く広げます
・その後、レジストに対してフォトマスク越しに光を当てます。フォトマスク越しに光を当てることで、フォトマスクに型取られたパターンがレジストに焼き付きます。
・光があたった部分のレジストは、光と反応していますので、現像液というものにつけることで取れたり、残ったりします。(感光した部分のレジストが取れるタイプをポジ型レジスト、感光した部分のレジストが固まって残るタイプをネガ型レジストといいます)
・これでフォトマスクのパターンがレジストにかたどられている状態になるので、シリコンウエハを削ったり、イオンを注入したり、いろいろと微細な加工ができる状態になります。
上記の一連の流れをまとめて「フォトリソグラフィー(Photo Lithography)」と読んだり、「写真製版」と呼んだりします。
フォトリソグラフィー[写真製版]工程は半導体チップを製造するために外せない工程であり、したがってフォトマスクも必須の部品なのです。
フォトマスクを作っているメーカー
・凸版印刷
・大日本印刷
フォトレジストを作っているメーカー
・東京応化工業(tok)
・JSR
・住友化学
・富士フイルムHD
・信越化学工業
4.プロセスを流して半導体チップをつくる
半導体製造装置とシリコン・ウエハなどの材料を揃えて、回路パターンが書き込まれたマスクが用意できて初めてプロセスを流していくことができます。
半導体チップを作っていくためには、「クリーンルーム」という非常にきれいでゴミがない部屋に、たくさんの半導体製造装置を並べて製造を行っていきます。
例えば、
・シリコン・ウエハをきれいに洗浄する
・温度1000度以上のめちゃくちゃ高温の炉の中にキレイなシリコン・ウエハを入れて、品質の高い酸化膜をつくる
・酸化膜にパターンをつけるために、フォトリソグラフィー(写真製版)をしてパターンを作る(これをパターニングという)
・パターニングした酸化膜を削る(エッチング[Etching]ともいいます)
・酸化膜を削った部分にイオン注入を行い、シリコンをn型、あるいはp型にする。
・もう一回別のマスクを使って、フォトリソグラフィーを行う。
などなど、たくさんの工程があります。
ひとつひとつ工程ごとに説明していきます。
前工程
洗浄工程
洗浄工程は、ウエハを薬液につけてウエハ表面をきれいにしたり、写真製版工程でついたレジストを除去したりする工程のことです。
洗浄工程に特化した半導体製造装置メーカーは、以下のとおりです。
・東京エレクトロン(日本)
・SCREEN ホールディングス(日本)
リソグラフィ(写真製版)工程
冒頭のフォトマスクのお話で触れた「写真製版工程」には、主に露光機という装置が必要になってきます。
露光機にマスクをセットして、マスク越しに光を当てる(露光する)。
こうすることで、レジストにマスクと同じパターンが形成される、という仕組みでした。
露光機を作っているメーカーは、下記のとおりです。
・ASML(オランダ)
・NIKON(日本)
・CANON(日本)
露光機の技術が、どのくらい微細なパターンを作ることができるかに極めて重要になってきます。
露光機メーカーの中でも特にASML(オランダ)の技術力が非常に高く、もっとも微細なパターニングができる技術を持っています。
ただし、装置価格も露光機一台あたり億単位のとんでもない金額がかかります。
世界一のファウンダーとして稼働している台湾のTSMCは、装置単価の高い装置を何台も納入していると言われています。
写真製版工程に関する詳細は下の記事でまとめています。
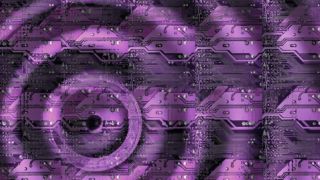
エッチング工程
エッチング(英語:Etching)工程は、化学反応を使って、酸化膜などを削る工程です。エッチングには2種類あって、ウェットエッチング(Wet Etching)とドライエッチング(Dry Etching)です。
ウェットエッチング
ウェットエッチングは、削りたい膜だけに反応する薬液にウエハを入れて、目的の膜を削るという工程です。ウェットエッチングはウエハの表面にダメージを残さず、きれいに目的の膜を削る事ができる特徴があります。
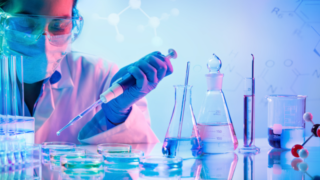
ドライエッチング
ドライエッチングは、薬液を使わずに削りたい膜だけを削る方法です。ではどうやるのかというと、チャンバーという金属の小さな部屋にウエハをいれて、そこを真空にして、削りたい膜と反応するガスを充満させて、電圧をかけて膜を削っていく、という原理です。
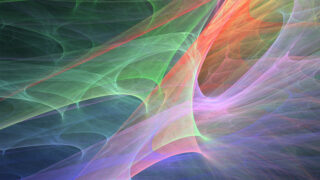
イオン注入工程
半導体は、不純物をいれることで真価を発揮します。
半導体にある特定の不純物を入れて、熱を加える(不純物を広げるため)と、
真性半導体からN型半導体やP型半導体に変化します。
P型半導体とN型半導体を接合させると、PN接合が形成され、
電気をある方向でのみ流すようにしたり(整流作用)、トランジスタとして
高速スイッチングができるデバイスにすることができます。
不純物を半導体中に導入するときに重要なのが、「イオン注入工程」です。
よく半導体への注入に利用される物質は、ボロン(Boron)やリン(P, Phosphorus)、ヒ素(As)などです。
イオン注入をするためには、イオン注入機という装置が必要です。
イオン注入機の装置メーカーはこちら
拡散工程
イオン注入をしたあとは、熱を加えて、導入した不純物を半導体の中へ拡散させていきます。
この工程を拡散工程と呼びます。
1000℃以上の熱をかけることもある工程です。
イオン注入をしただけでは、PN接合を形成したとは言いがたく、
イオン注入したあとに、熱拡散工程を経ることで不純物領域(P型半導体領域だったり、N型半導体領域だったり)を形成することができます。
酸化膜成膜工程
拡散工程にはもうひとつの役割もあります。
それは熱酸化膜を形成する役割です。
半導体(シリコン)に酸素雰囲気で高温の熱拡散をすることで、
非常に良質な熱酸化膜(絶縁膜)を得ることができます。
この絶縁膜の出来がいいので、高品質なトランジスタを大量生産することができます。
金属成膜工程
その後、前工程の仕上げとして金属を成膜する「金属製膜工程」があります。
この金属が電極になります。
後工程
ここからは、半導体の「後工程」と呼ばれる領域について書いていきます。
バックグラインド(裏面研削)工程
半導体では、裏面を削る(研削する)バックグラインド工程というものがあります。
↓バックグラインド工程に関する情報をまとめた記事はこちらです(^^)↓
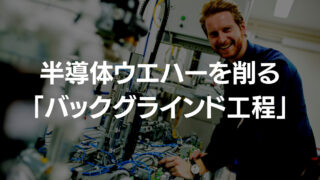
ダイシング工程
「ダイシング工程」は、円盤状になっているシリコンウエハーをチップ形状に切り出していく工程のことです。
↓ダイシング工程に関する情報をまとめた記事はこちらです(^^)↓
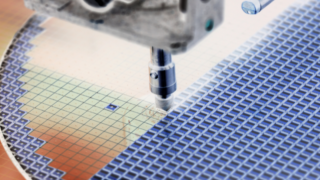
リードフレームについて
↓リードフレームに関する情報をまとめた記事はこちらです(^^)↓
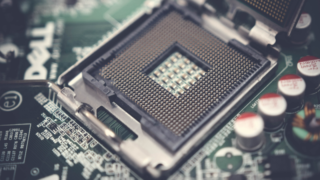
ボンディング工程
ボンディング工程の詳細は下記の記事にまとめております。
↓ボンディング工程に関する情報をまとめた記事はこちらです(^^)↓
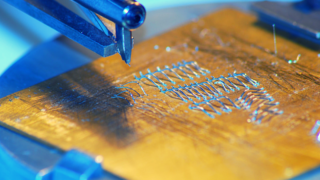
さらに、超音波ボンディングについては下記の記事にまとめております。
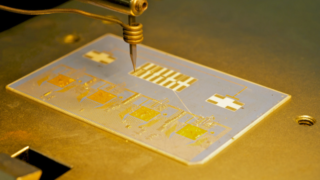
樹脂封入工程
樹脂封入工程は、半導体チップが格納されたパッケージのなかに、エポキシ樹脂を流し込み、硬化させる工程です。
これによって半導体チップの信頼性が向上します。
↓樹脂封入工程に関する情報をまとめた記事はこちらです(^^)↓
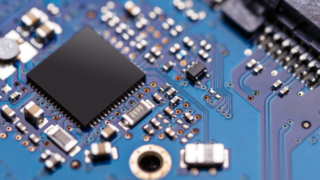
タイバーカット工程
タイバーカット工程の由来は、ネクタイピン(Tie Bar)から来ています。
リードフレームにはここから切り離してくださいね、という領域がもうけてあり、そこをタイバーと表現します。
そのタイバー部分をカットするので、タイバーカット工程といいます。
↓タイバーカット工程に関する情報をまとめた記事はこちらです(^^)↓
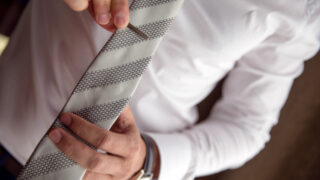
バリ取り工程
バリ取り工程とは、後工程で発生した樹脂バリ(フラッシュ)を除去する工程です。
↓バリ取り工程に関する情報をまとめた記事はこちらです(^^)↓
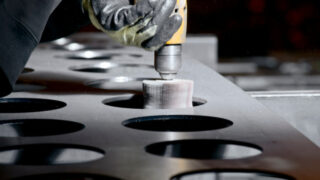
メッキ工程
捺印工程
リード加工工程
パッケージング工程
テスト工程
テスト工程に特化した半導体テストメーカーは以下のとおりです。
・アドバンテスト
最先端のロジック半導体(例:パソコンのCPU(Central Processing Unit))には、数十枚のマスクが使われています。